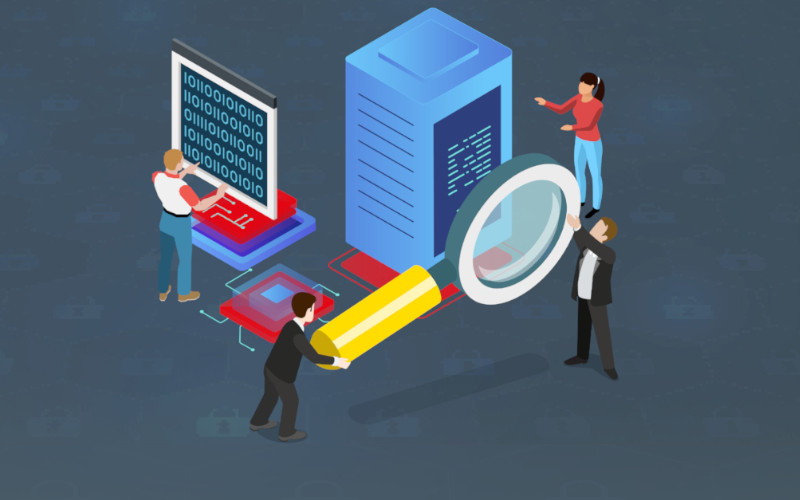
Firmware analysis can help to uncover potential vulnerabilities that would otherwise never have been discovered.
Although there are multiple types of attacks on IoT and IIoT devices, this guide focuses on the firmware of these devices to check for potential vulnerabilities, using security testing and reverse engineering to allow for an in-depth analysis of the firmware.
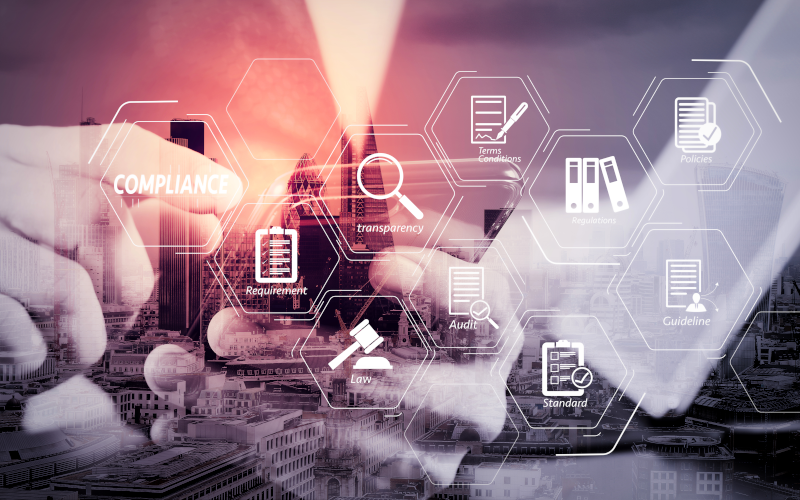
Information security standards have become increasingly important in recent years, as more and more legal requirements oblige companies to demonstrate a certain degree of cybersecurity compliance. The IEC 62443 family of standards describes in its various sections the requirements for the secure implementation of an ICS (Industrial Control System) and represents a guarantee of cybersecurity in industrial environments. This article deals with IEC62443-3-3 covering cybersecurity of industrial systems.
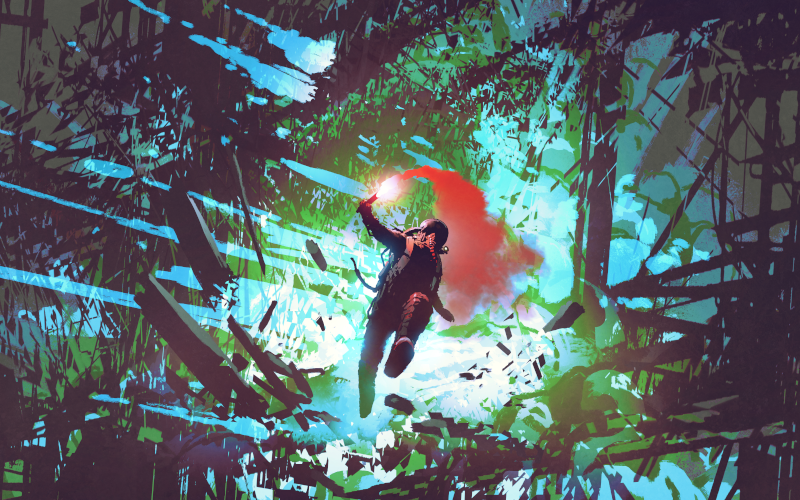
The increase of malware specifically designed to run on systems that support industrial processes creates a need in the industry that can be partly covered by different technological solutions. This article will focus on the different options available on the market to detect malicious files that aim to modify the operation of industrial environments or simply cause denials of service.
Both portable and agent-deployed solutions can be an option, and this article will reflect on these and other options as well as provide guidelines on when it is best to use one solution or the other.
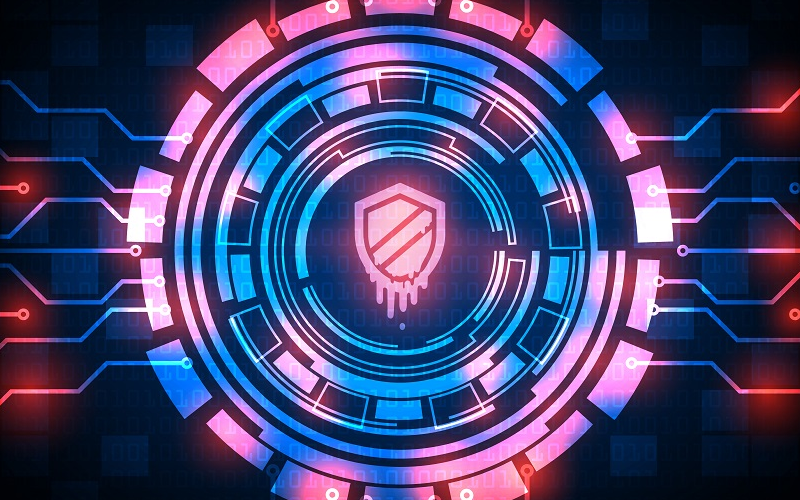
Within the industrial world, systems can be detected that do not have all their cybersecurity capabilities activated. This can occur for a variety of reasons, but if detected, each case must be analyzed to get the most out of each device.
The ability to robustly configure programs, services or other nuances within industrial systems is called bastioning and allows, among other things, to prevent assets from having a large exposure to the network or the solutions deployed in the system from having vulnerabilities resulting from misconfiguration.
In this article, we will begin by explaining what hardening is and how to apply it to our industrial network, along with some good practices to follow.
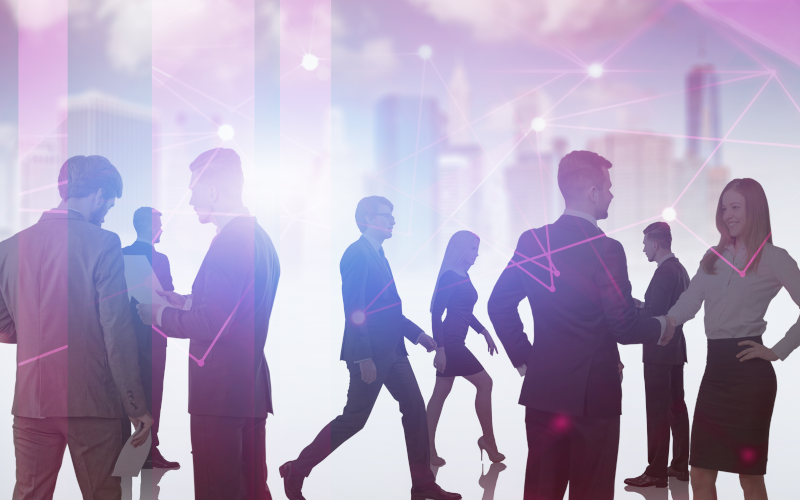
The Purple Teams are exercises in which three very well differentiated teams participate: a Red Team, a Blue Team and a Purple Team. The Red Team will be in charge of carrying out attacks on the defined structure, the Blue Team will be the team in charge of defending that structure and the inclusion of the Purple Team allows the two previous teams to communicate with each other and be organized correctly thanks to the work of the purple team. This is why the Purple Teams allow a great number of advantages to be obtained with respect to carrying out the exercises separately and without coordination between them.
This article presents all these advantages and much more about Purple Teams.
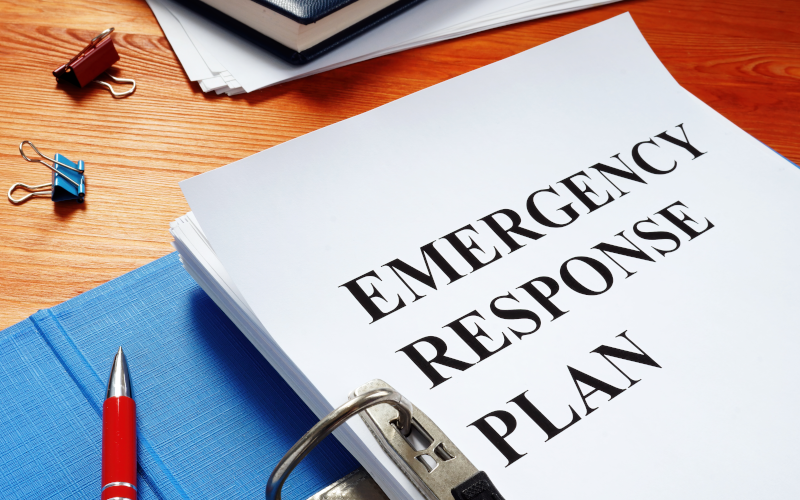
When a security incident occurs in an ICS (Industrial Control System), depending on the severity of the incident, it can generate a serious problem, both at a productive and economic level, as well as in the security of the people working in the industrial system.
Therefore, in this article following the one entitled "Good practices for the recovery of industrial systems (I)", response plans will be discussed from a point of view oriented to current regulations, as well as their applications and necessity in critical industrial environments, such as the energy sector.
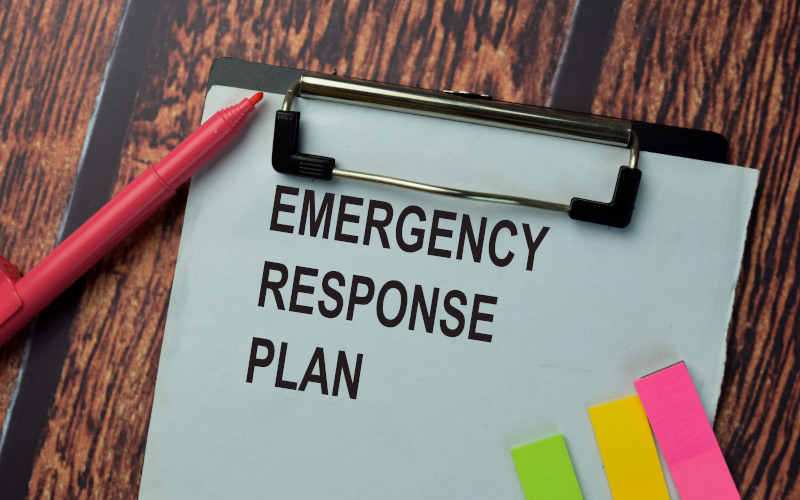
When a security incident occurs in an ICS (Industrial Control System), depending on its severity, it can generate a serious problem, both at a productive and economic level, as well as in the security of the people working in the industrial system.
Therefore, in this first article of a series on this subject, we will explain precisely the recovery plans, some general guidelines for their development and some conclusions on the use and applicability of these plans.
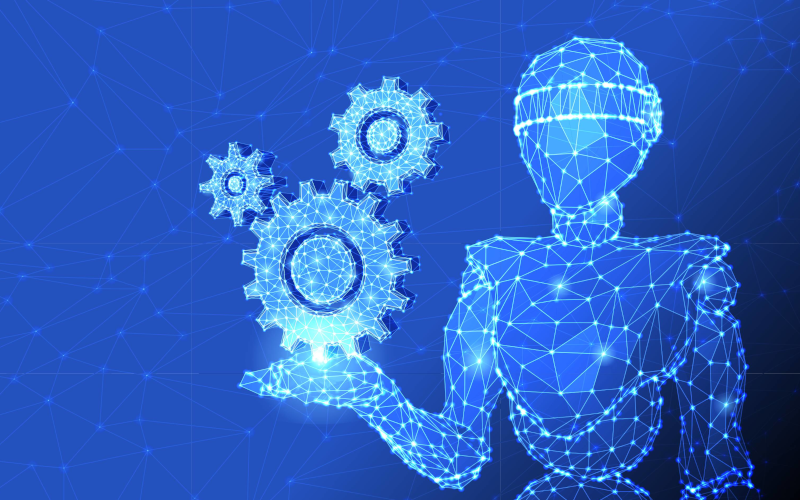
In recent years, the constant technological evolution has made possible a large number of advances that would have been unthinkable years ago. In industrial environments, one of the latest developments that promises to stand out and is here to stay are virtual PLC.
The virtualization of these controllers will make it possible to decouple the hardware from the software, i.e. the software will be installed in the engineering stations, while the hardware will remain in another area outside the production area.
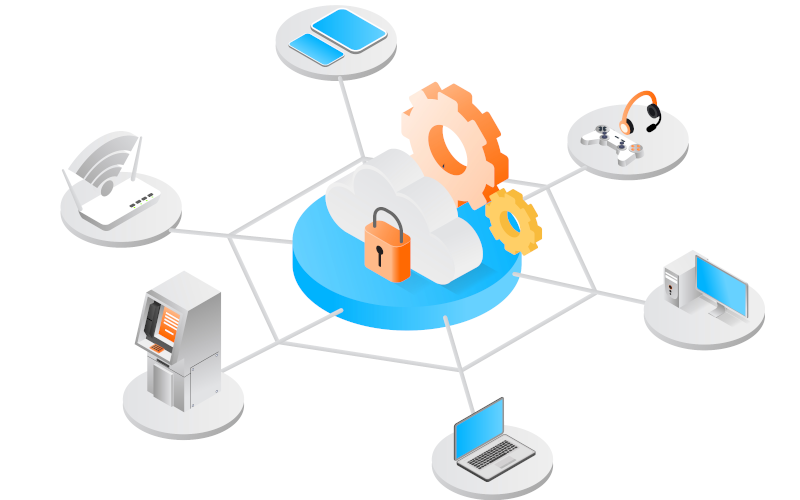
IDSs are passive elements that are in our network to ensure its security, but what would happen if all our communications were encrypted, or would this protection measure be enough to ensure that my network is protected? These questions and more will be discussed in the following article to provide solutions and advice focused on industrial environments.
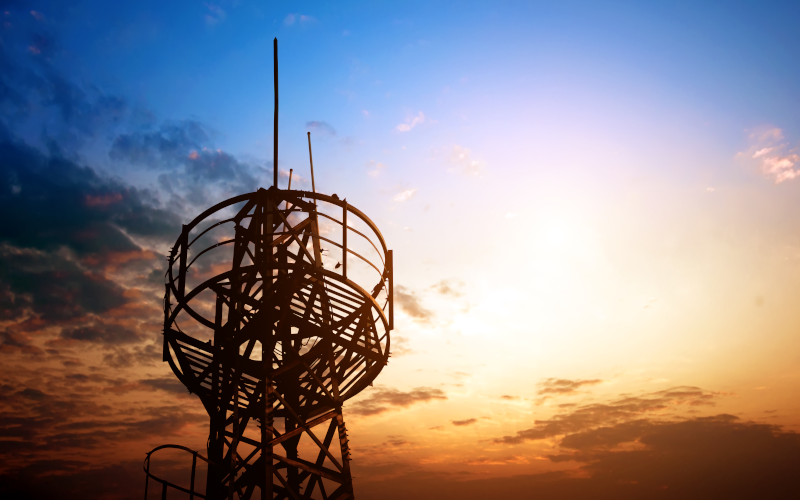
The Industrial Internet of Things (IIoT) has experienced considerable growth in recent years, providing crucial improvements. However, it also has some limitations in terms of consumption, security, cost or scalability. In this blog, we will see how the appearance of LoRaWAN in this area can solve part of those limitations.