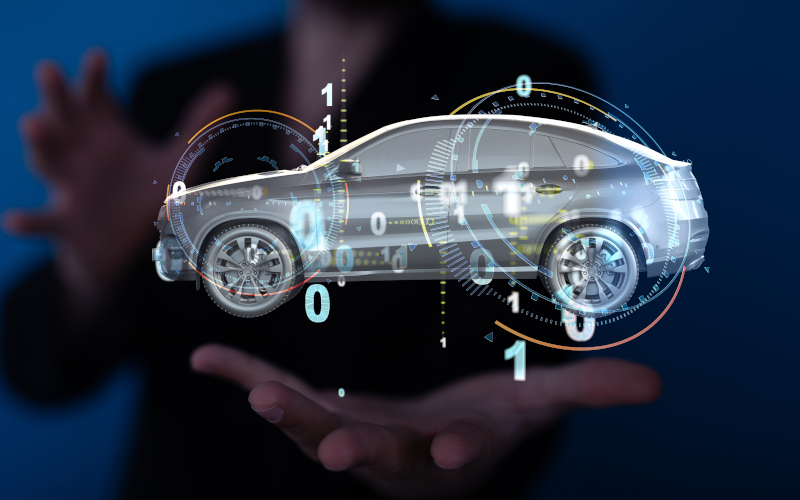
This article aims to present a brief example guide for an implementation of the new standard in a supplier's facilities.
Going through the critical points of the standard, a generic use case will be followed to exemplify how a vehicle manufacturer can adapt its processes to comply with the new standard in an efficient and effective way.
By presenting an overview of the standard and production processes, the aim is to provide a brief guide to serve as a starting point and help avoid common failures in industrial environments when faced with new regulations, such as redundancy of effort, inefficiency in resource management and deficiencies in the application of safety measures.
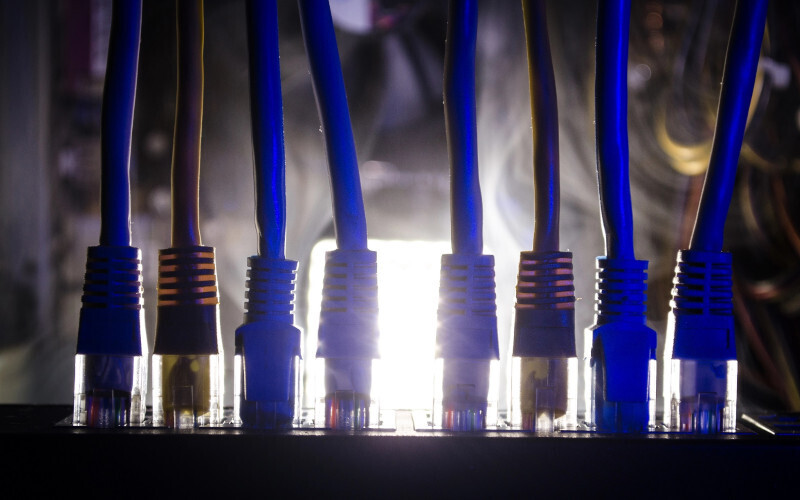
Larger scale and complexity industrial control networks present risks, and cybersecurity needs that usually cannot be met by applying a traditional segmentation model. Factors such as the presence of critical obsolete equipment, equipment managed by third parties or the increased presence of IoT technologies that require external connections, are motivating the adoption of more advanced architectures when applying the principle of defense in depth.
Proper segmentation can be a fundamental aspect in preventing attacks, especially in their propagation to essential and critical production assets. It is also important to adapt to the environment to be segmented. It is a common mistake to try to segment networks based on concepts and schemes like the IT environment.
This article will present some new network models and tips to work on a correct segmentation in an environment where different components are involved (OT, IIoT, IT, IoT).
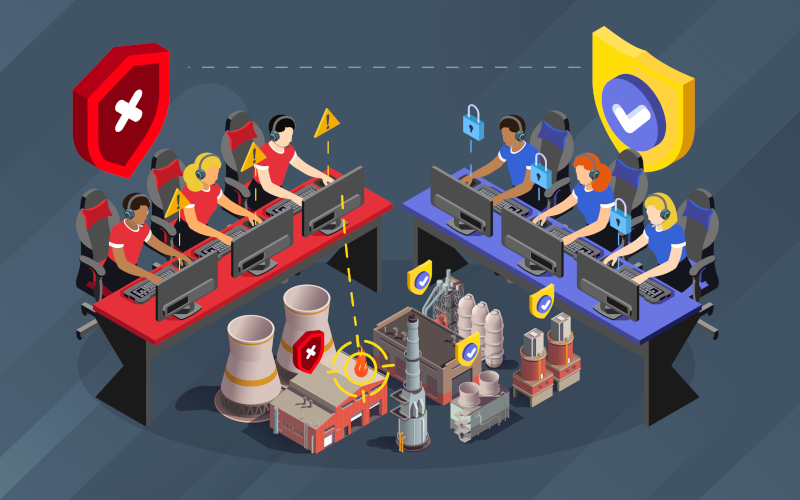
MITRE Caldera OT stands out mainly for being an open-source tool that allows the simulation of different cyber-attacks in industrial environments. This tool was created by MITRE and CISA (US Cybersecurity and Infrastructures Security Agency), as the experts saw the need to be able to improve and understand cybersecurity in industrial environments without using a high number of resources.
In addition, this tool is designed to be used by both the Red Team and the Blue Team, allowing both teams to collaborate with each other to improve the level of cyber security in these environments.
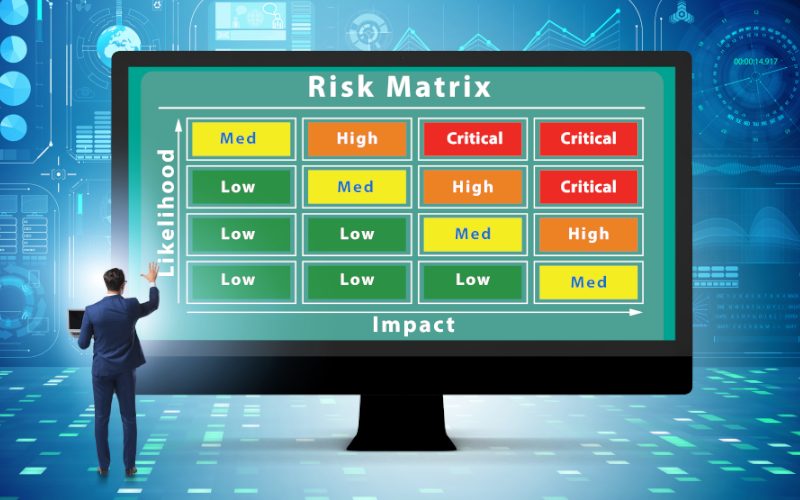
In the era of interconnection and digitization, industrial control systems (ICS) are increasingly exposed to cyber threats. These systems are vital for energy production, manufacturing and critical infrastructure management, and their protection has become an essential priority.
Risk analysis is fundamental in this context, as it allows identifying, assessing and prioritizing the risks that can affect ICS. This process, ranges from technical vulnerabilities to emerging threats, and is crucial for developing effective mitigation and protection strategies.
In this article, the challenges and solutions related to risk analysis in ICS will be explored, as well as the importance of the IEC 62443-3-2 standard in this critical process.
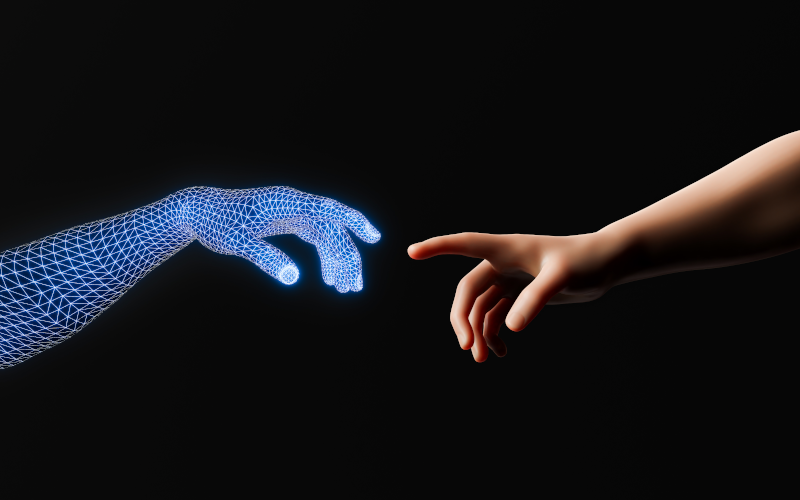
The digital twins are virtual recreations of real-world objects or processes. This innovative idea, proposed by Dr. Michael Grieves, has become increasingly relevant in various industrial sectors thanks to the advancement of technologies such as 3D modelling, the Internet of Things (IoT), the IIoT (Industrial Internet of Things), machine learning and big data. Its application makes it possible to simulate and analyse physical processes efficiently, thus contributing to the digital transformation of industry, also known as Industry 4.0.
The fundamental purpose of digital twins is to facilitate the understanding of how elements operate in the physical world. For example, in manufacturing, it is possible to create a digital twin of a factory and through simulations explore different scenarios: what would happen if a machine were modified, how would it impact production, and what would happen if a machine were changed? The digital twin provides answers before real changes are made to the physical environment, speeding up decision-making and optimising processes.
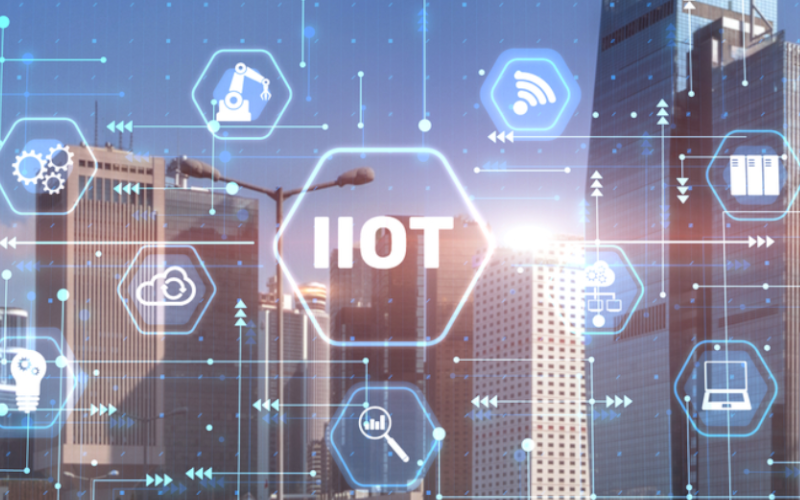
In today's business landscape, the digital revolution has led to an unprecedented transformation, and at the epicenter of this evolution are Industrial Internet of Things devices (IIoT). These devices, skilled in collecting and transmitting data in real-time, have emerged as fundamental pillars, that drive operational efficiency and decision-making in industrial environments.
From advanved sensors to smart sctuators, the network of IIoT devices implemented in the industrial fabric is improving the frontiers of connectivity, impacting the way companies design, implement, and manage their operations.
In this article, we will learn about the role of these devices within Industry 4.0, analyzing how different types of architectures are implemented and how their communications protocols shape the future of the industry.
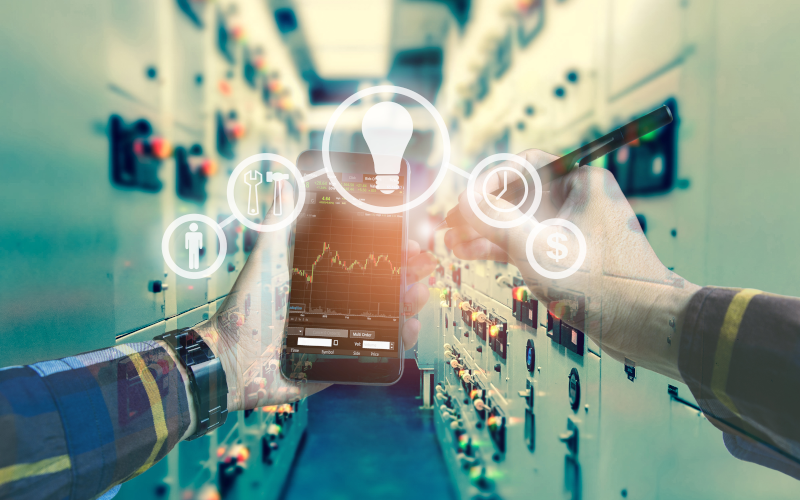
In the electricity sector, it has always been necessary to use robust communications that allow proper communication, since a failure in this sector would cause a large number of losses, both economic and social.
In addition, with the technological advances, it is important also to have secure communications since the electricity sector is one of the sectors that currently suffers the most cyber-attacks. For this reason, in recent years different robust and secure protocols have been created.
One of these protocols is DNP3, created mainly for the use of substation automation and control systems, for the electric utility industry, although it has now also been used for other sectors.
Finally, in this article we want to explain in more depth the operation of this protocol and the benefits or disadvantages of using this protocol.
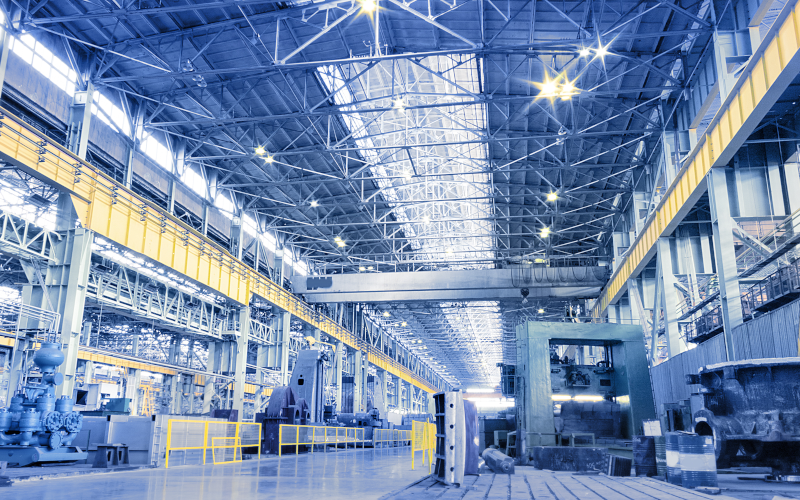
CAPEC (Common Attack Pattern Enumeration and Classification) is a project that focuses on enumerating and classifying common attack patterns on computer systems and providing a systematic approach to understanding and addressing the tactics used by attackers. Like CWE (Common Weakness Enumeration), CAPEC is an initiative of the computer security community and is maintained by the National Institute of Standards and Technology (NIST) in the United States. Recently in version 3.9, the project has incorporated a number of attack patterns related to the industrial world.
This article aims to show the reader the use of these codes, such as those used at the identifier level in CVEs, CWEs, etc., and which are related to many of the jobs that are carried out on a daily basis in the industrial cybersecurity sector.
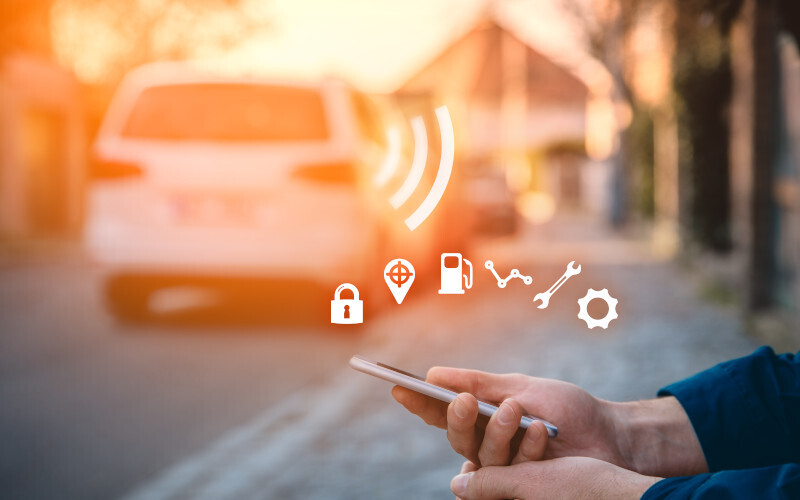
The automotive world has always been one of the most cutting-edge sectors in terms of the technology used, which is why today's cars are equipped with technologies such as Bluetooth, NFC, GPS, etc., which improve different aspects such as comfort, fuel efficiency and increased safety.
But these implemented technologies can also bring with them serious problems, such as the risk of cyber-attacks that can affect passengers in the vehicle, both at the level of personal data and physical security.
For this reason, this article aims to provide an insight into some of the cyber-attacks that smart cars have suffered and how cyber-security is evolving and adapting to make more and more vehicles cyber-safe.
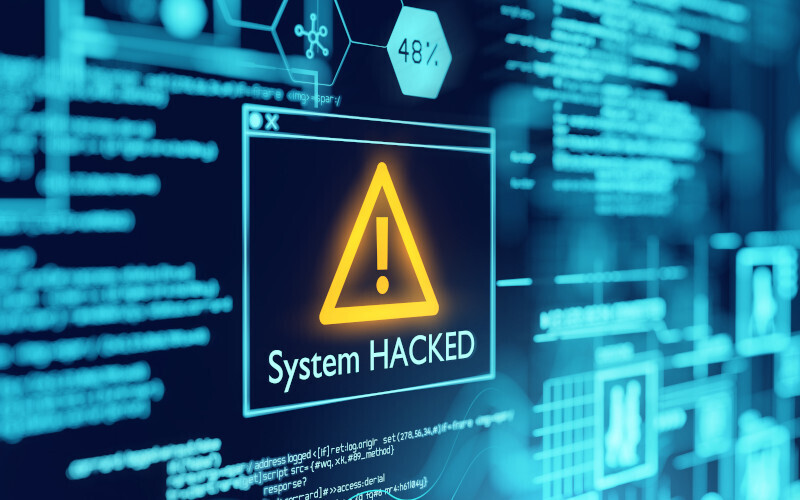
Currently, industrial infrastructures are suffering more attacks than ever before, and it is expected that attacks on these types of infrastructures will continue to grow exponentially in the coming years. This is why, throughout this article, an analysis will be made of a group of cybercriminals and their standard attack, showing how information can be obtained on the modus operandi, when and by what tactics and techniques they managed to attack an industrial infrastructure