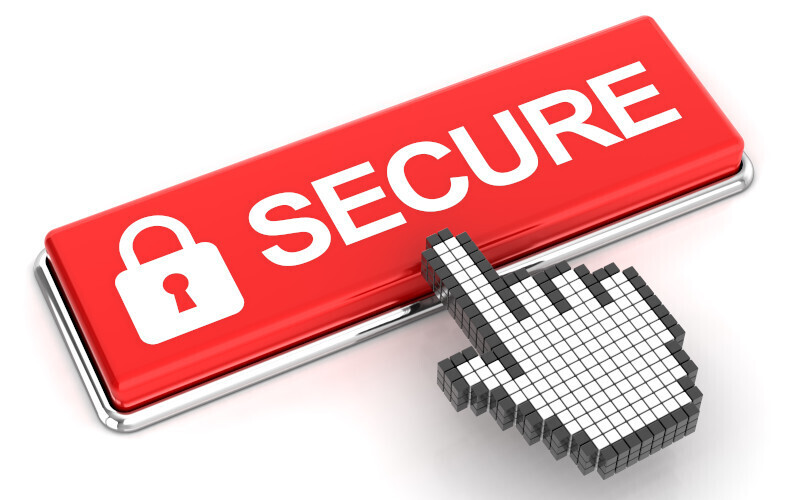
Segunda parte del ‘Top 20 mitigaciones para entornos industriales’. Esta parte se focalizará en mitigaciones relacionadas con la arquitectura de red, los protocolos industriales, la configuración de redes y el escaneo de vulnerabilidades.
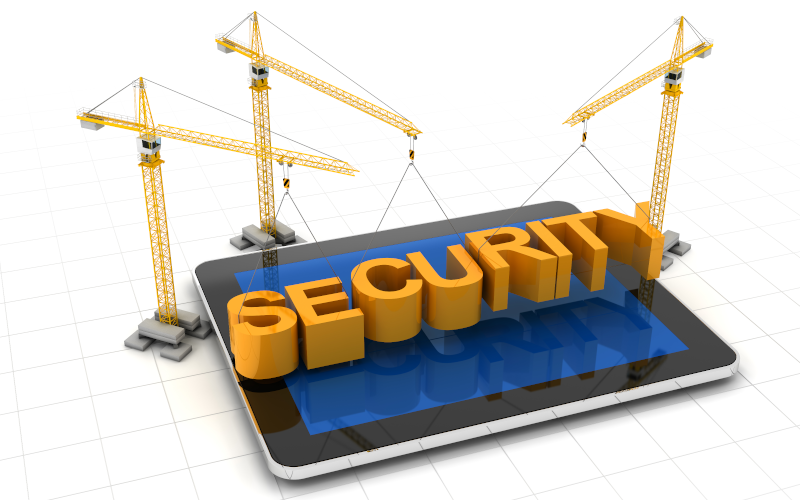
En el mundo industrial existen una gran cantidad de sistemas, equipos, redes, zonas, conductos, entornos cloud, entornos IT-OT, etc. En los últimos años, el número de ataques sobre entornos industriales ha ido creciendo exponencialmente, y ya no solo sobre entornos puramente industriales, sino también sobre los entornos corporativos que tienen conexión con entornos industriales, siendo estos entornos IT, puntos de acceso para los atacantes debido a esa conectividad IT/OT.
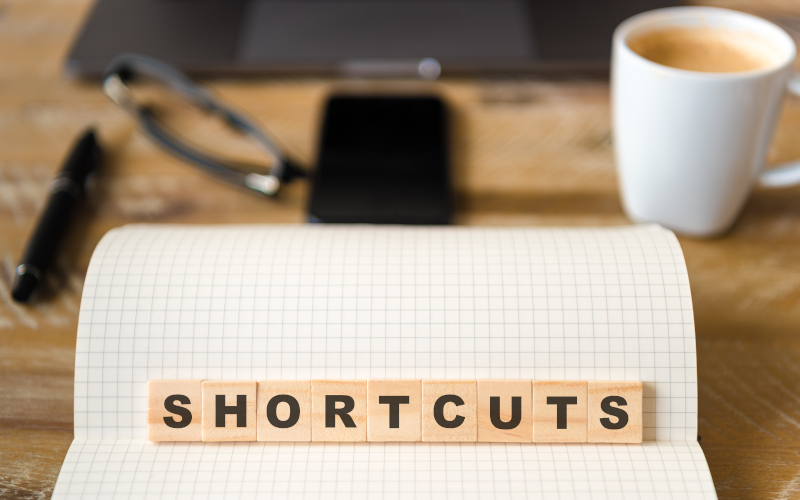
La presencia de Shadow IT, es decir, el uso no autorizado o no gestionado de tecnologías y servicios de TI por parte de los empleados, plantea desafíos y riesgos de considerable magnitud.
La rápida adopción de dispositivos y aplicaciones personales, así como la accesibilidad a servicios en la nube, han incrementado la complejidad del panorama de seguridad. Esta situación supone un riesgo que puede comprometer la confidencialidad y la integridad de la información de la organización.
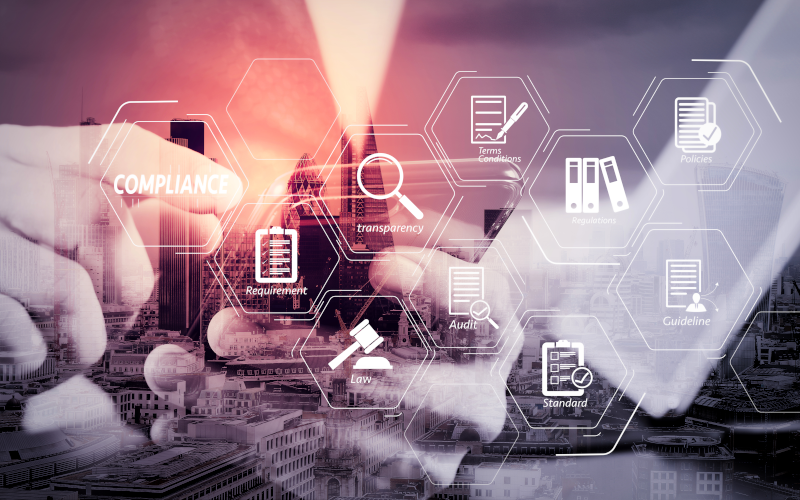
Los estándares de seguridad de la información han adquirido gran protagonismo en los últimos años, debido a que cada vez son más los requisitos legales que obligan a las empresas a acreditar cierto grado de cumplimiento en ciberseguridad. La familia de estándares IEC 62443 describe en sus varias secciones, los requisitos de implementación segura de un sistema ICS (Industrial Control System, de sus siglas en inglés) y representa una garantía de ciberseguridad en entornos industriales. Este articulo trata sobre la IEC62443-3-3 que cubre la ciberseguridad de sistemas industriales.
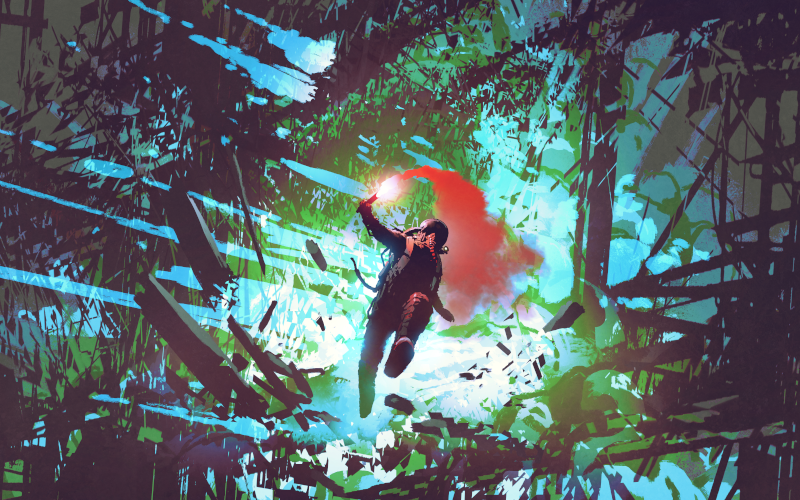
El incremento de malware específicamente diseñado para ejecutar sobre sistemas que soportan procesos industriales crea una necesidad en la industria que puede cubrirse en parte con diferentes soluciones tecnológicas. Este artículo se centrará en las diferentes opciones disponibles en el mercado para poder detectar archivos maliciosos que tienen como objetivo modificar el funcionamiento de los entornos industriales o simplemente originar denegaciones de servicio.
Tanto las soluciones portables como las desplegadas por agente en los sistemas pueden ser una opción, en este artículo se verán reflejadas estas y otras opciones al igual que también se darán unas pautas de cuándo es mejor utilizar una solución u otra.
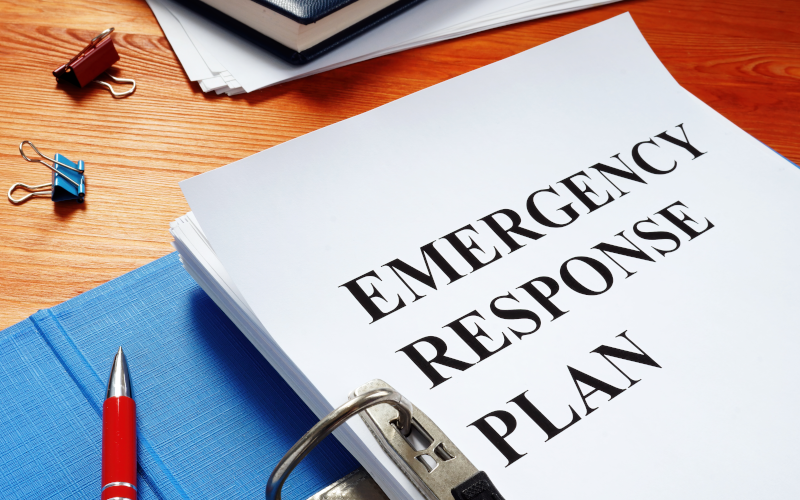
Cuando se produce un incidente de seguridad en un SCI (Sistema de Control Industrial), dependiendo de la gravedad del mismo, se puede generar un grave problema, tanto a nivel productivo, como económico o en la seguridad de las personas que trabajan en el sistema industrial.
Por lo tanto, en este artículo sucesivo al titulado “Buenas prácticas para la recuperación de sistemas industriales (I)”, se tratarán los planes de respuesta desde un punto de vista orientado a las normativas actuales, así como sus aplicaciones y necesidad en entornos industriales críticos, tales como el sector energético.
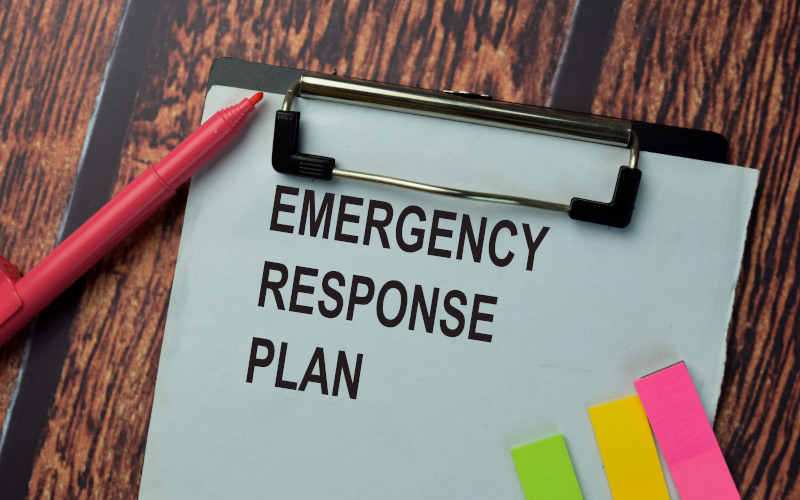
Cuando se produce un incidente de seguridad en un SCI (sistema de control industrial), dependiendo de la gravedad del mismo, se puede generar un grave problema, tanto a nivel productivo como económico o en la seguridad de las personas que trabajan en el sistema industrial.
Por lo tanto, en este primer artículo de una serie destinada a esta materia, se explicarán de forma precisa los planes de recuperación, unas pautas generales para su desarrollo y unas conclusiones sobre el uso y la aplicabilidad de estos planes.
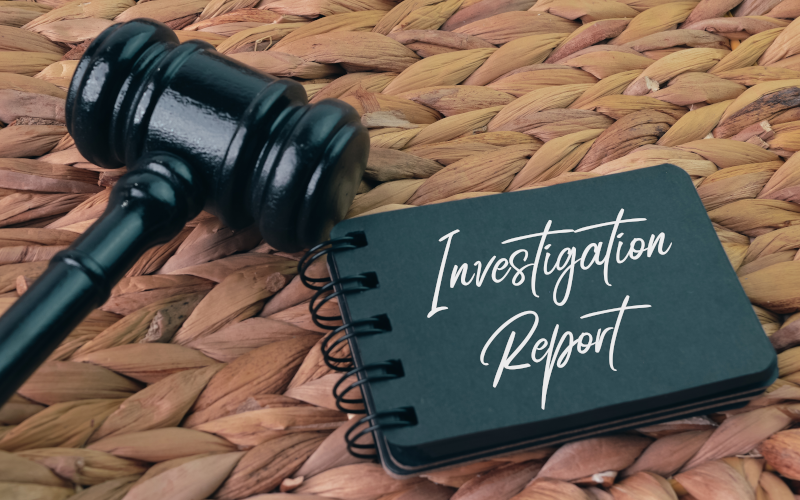
La elaboración de informes técnicos es una de las partes más importantes para la conclusión de una tarea, ya que refleja los resultados de todo el trabajo realizado. Además, no solo constituye un entregable final para un cliente, o para los responsables de una institución, sino también es el nexo de unión entre la persona o equipo que ha llevado a cabo dicha tarea y los responsables de la toma de decisiones, en base a los hallazgos encontrados.
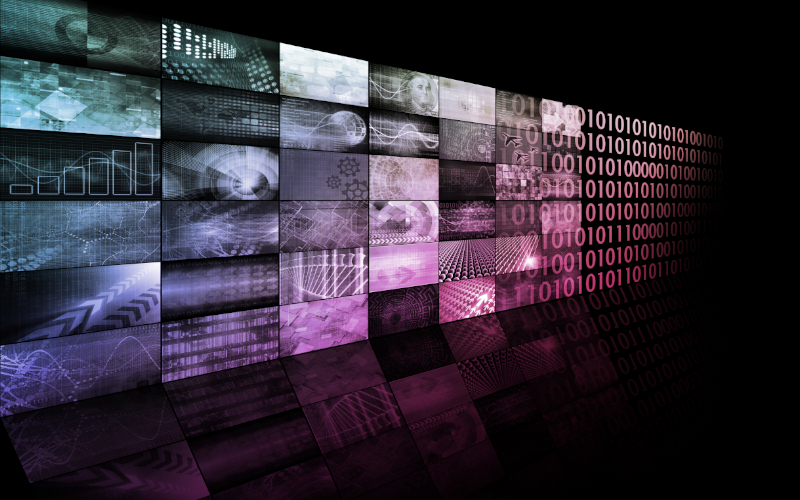
En la actualidad, existe una constante evolución en las tecnologías e implementaciones realizadas en los Sistemas de Control Industrial. Unas de las implementaciones más comunes para la mejora de las infraestructuras de sistemas industriales son la digitalización y el uso de la tecnología cloud. Por otra parte, el aumento de los protocolos de comunicación y los dispositivos IIoT (debido al crecimiento de la Industria 4.0) genera un gran volumen de tráfico difícil de controlar y securizar.
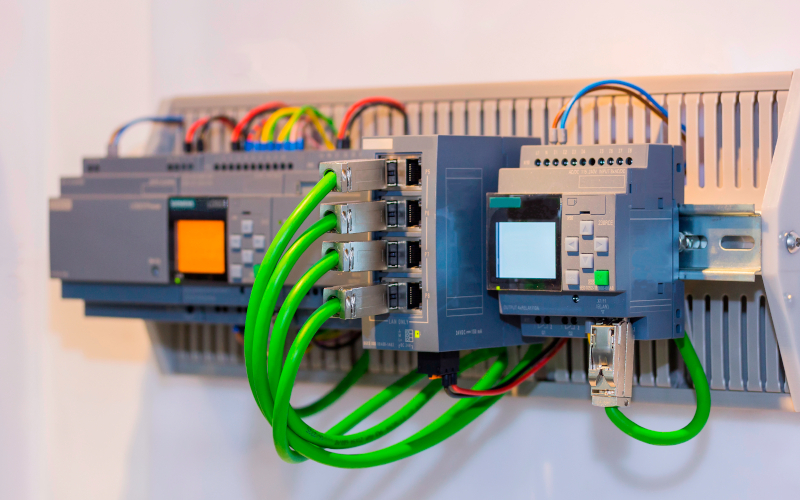
La programación de los PLC es una parte fundamental en las fases iniciales cuando se construyen y diseñan las plantas industriales. Sobre dicho entorno, la compañía basará la totalidad de sus operaciones, con lo cual la configuración de estos controladores es un aspecto crítico. A la hora de programar estos dispositivos, existe una serie de pautas y buenas prácticas que aprovechan funcionalidades disponibles de forma nativa y que implican poco o ningún recurso a mayores de los que posee un programador de PLC, protegiendo al dispositivo de una forma sencilla y con un mínimo gasto de recursos.